Другие статьи: | ||
Присутствие NTN-SNR и успех её продукции на отраслевых рынках | ||
Обучение | ||
Отзывы о Подшипник.ру | ||
Каталоги NTN-SNR | ||
ВАКАНСИИ |
||
какие подшипники вы используете |
Монтаж подшипников
Для подготовки подшипников к монтажу предварительно проверяют надписи на упаковке и самих подшипниках.
Распаковывают подшипники непосредственно перед началом работ с ними.
Расконсервацию подшипников производят согласно действующей инструкции по хранению, расконсервации подшипников и их деталей и обращению с ними. Как правило, подшипники расконсервируют в горячем (80-90 °С) минеральном масле, тщательно промывают в 6-8%-ном растворе масла, в бензине или в горячих (75-85°С) антикоррозионных водных растворах, например, следующих составов (в %-тах):
Раствор N1 |
Раствор N2 |
|
Триэтаноломин |
||
Нитрит натрия |
||
Смачиватель ОП |
||
Остальное |
Остальное |
Хранить расконсервированные подшипники более двух часов без защиты от коррозии не рекомендуется.
После расконсервации потребитель подшипников должен обеспечить их защиту от коррозии при контроле, монтаже, сборке и хранении изделий по соответствующей внутризаводской инструкции.
Перед монтажом подшипник следует проверить на соответствие внешнего вида, легкости вращения, зазоров требованиям нормативно-технической документации.
Визуально у подшипников открытого типа должны быть проверены наличие забоин, следов загрязнений, коррозии, полного комплекта заклепок, плотности их установки или других соединительных элементов, полного комплекта тел качения, наличие повреждений сепаратора.
У подшипников закрытого типа следует проверить не повреждены ли уплотнения или защитные шайбы.
Для проверки радиального зазора одно из колец подшипника закрепляют при горизонтальном положении оси и определяют зазор с помощью индикатора, смещая свободное кольцо под действием измерительного усилия в радиальном направлении в два диаметрально противоположные положения. Разница показаний прибора соответствует значению радиального зазора. Проводят три измерения, поворачивая свободное кольцо относительно начального положения оси подшипника. Аналогично проводят измерение осевого зазора, но при вертикальном положении оси подшипника. Закрепляя одно из колец, другое смещают в осевом направлении в два крайних положения под действием измерительного усилия и фиксируют разность показаний индикатора. Радиальные зазоры в радиальных двухрядных сферических роликовых подшипниках и подшипниках с цилиндрическими роликами без бортов на наружных кольцах с диаметром посадочного отверстия свыше 60 мм могут быть измерены с помощью щупа.
Непосредственно перед монтажом необходимо проверить монтажные поверхности корпусов (отверстия и торцы) и валов (посадочные поверхности и торцы) на отсутствие забоин, царапин, глубоких рисок от обработки, коррозии, заусенцев и загрязнений.
Валы, особенно при соотношениях длины и наибольшего диаметра более 8, следует проверять на прямолинейность оси (отсутствие изгиба). Проверку целесообразно проводить при вращении вала в центрах с помощью индикаторов часового типа. Увеличение эксцентриситета в направлении от края к середине указывает на искривление вала.
Необходимо проверить отклонение от соосности всех посадочных поверхностей, расположенных на одной оси, на соответствие нормам, указанным в технической документации.
Если подшипники, служащие опорой одного вала, устанавливают в различные (раздельные) корпуса, соосность корпусов, в соответствии с требованиями технической документации, должна быть обеспечена с помощью прокладок или других средств.
При установке на одну посадочную шейку двух подшипников (радиальных: шариковых, роликовых сферических и цилиндрических) разница в радиальных зазорах не должна превышать 0,03 мм, а по внутреннему и наружному диаметрам колец - не более половины поля допуска.
Сопрягаемые с подшипниками поверхности валов и корпусов должны быть тщательно промыты, протерты, просушены и смазаны тонким слоем смазочного материала или антифреттингвой пастой. Каналы для подвода смазки должны быть очищены от стружки и других загрязняющих частиц и продуты сжатым воздухом.
При монтаже подшипника усилие напрессовки должно передаваться только через напрессовываемое кольцо - через внутреннее при монтаже на вал и через наружное - в корпус. Запрещается проводить монтаж таким образом, чтобы усилие передавалось с одного кольца на другое через тела качения. Если подшипник одновременно монтируется на вал и в корпус, то усилия передаются на торцы обоих колец.
Не допускается приложение монтажных усилий к сепаратору. Нельзя наносить удары непосредственно по кольцу. Допускается нанесение легких ударов по кольцу только через втулку из незакаленной конструкционной стали.
При монтаже подшипников с цилиндрическим отверстием на вал с натягом подшипник целесообразно предварительно нагреть на индукционном нагревателе.
Нагретый подшипник устанавливают на вал и доводят до места небольшим усилием. При этом сторона подшипника, на которой нанесено заводское клеймо, должна быть снаружи.
Для монтажа крупногабаритных подшипников наиболее целесообразным является применение гидравлического распора, обеспечивающего наиболее качественную установку подшипника, отсутствие каких-либо повреждений монтажных поверхностей и высокую производительность. Особенно целесообразен этот способ для монтажа подшипников с внутренним коническим отверстием диаметром более 120-150 мм.
При посадке подшипника в корпус с натягом рекомендуется перед монтажом предварительно охладить подшипник жидким азотом (-160 °С) или сухим льдом, либо нагреть корпус.
Наиболее целесообразными являются способы монтажа, при которых осуществляется одновременное и равномерное давление по всей окружности монтируемого кольца. При таких способах не возникает перекос монтируемого кольца. Для осуществления подобных способов применяют трубы из незакаленной конструкционной стали, внутренний диаметр которых несколько больше диаметра отверстия кольца, а наружный немного меньше наружного диаметра кольца. На свободном конце трубы следует установить заглушку со сферической наружной поверхностью, к которой и прилагают усилие при монтаже.
Усилие при монтаже следует создавать с помощью механических либо гидравлических прессов и приспособлений.
При отсутствии механических и гидравлических приспособлений и монтаже с небольшими натягами подшипников малых размеров допустимо нанесение несильных ударов молотком через монтажную трубу с заглушкой.
При любых способах монтажа, особенно при монтаже с помощью молотка, необходимо тщательно следить за обеспечением равномерного, без перекоса, осевого перемещения кольца. Наличие перекоса при монтаже приводит к образованию задиров на посадочной поверхности, неправильной установке подшипника, приводящей к сокращению срока его службы, а в отдельных случаях - к разрыву монтируемого кольца.
Двухрядные сферические шариковые и роликовые подшипники с коническим отверстием устанавливают на цилиндрическом валу с помощью закрепительных и стяжных втулок, а на валах с конической шейкой - непосредственно на шейку вала. Монтаж подшипников с диаметром отверстия до 70 мм и нормальными натягами целесообразно осуществлять с помощью монтажной втулки, навертываемой на резьбовой конец вала. Нажимная часть воздействует на торец закрепительной втулки или непосредственно на торец внутреннего кольца (при монтаже без закрепительных и стяжных втулок). Подшипники с диаметром отверстия свыше 70-100 мм следует монтировать гидравлическими методами. Так как по мере осевого продвижения закрепительной втулки внутреннее кольцо подшипника деформируется (расширяется), радиальный зазор уменьшается. Радиальный зазор необходимо контролировать с помощью щупа. Допустимое минимальное значение радиального зазора в миллиметрах после сборки узла для подшипников, изготовленных с зазорами нормальной группы по ГОСТ 24810, ориентировочно может быть определено по формуле
где d - номинальный диаметр отверстия подшипника, мм.
Крупногабаритные (с диаметром отверстия более 300 мм) сферические роликовые подшипники целесообразно перед монтажом разогреть до 60-70°С,
При монтаже игольчатого подшипника без сепаратора последняя игла должна входить с зазором, равным от 0,5 до 1 диаметра иглы. Иногда для выполнения этого условия устанавливают последнюю иглу с меньшим диаметром.
В процессе установки подшипников (особенно воспринимающих осевые усилия) там, где это возможно, с помощью щупа толщиной от 0,03 мм или по световой щели следует убедиться в плотном и правильном прилегании торцов колец подшипника к торцам заплечиков. Аналогичной проверке должны быть подвергнуты противоположные торцы подшипников и торцы прижимающих их в осевом направлении деталей.
Необходимо проверить правильность взаимного расположения подшипников в опорах одного вала. Вал после монтажа должен вращаться от руки легко, свободно и равномерно.
Осевой зазор радиально-упорных и упорных подшипников устанавливают осевым смещением наружного и внутреннего колец с помощью прокладок, гаек, распорных втулок. Для проверки осевого зазора в собранном узле к торцу выходного конца подводят измерительный наконечник индикатора, укрепленного на жесткой стойке. Осевой зазор определяют по разнице показаний индикатора при крайних осевых положениях вала. Вал смещают в осевом направлении до полного контакта тел качения с поверхностью качения соответствующего наружного кольца.
Для повышения точности вращения, особенно в быстроходных узлах, например, станочных электрошпинделях, зазоры в радиально-упорных подшипниках выбирают, создавая стабильный преднатяг на подшипники. Это достигается приложением к вращающемуся кольцу подшипника осевого усилия через тарированную пружину. При этом тела качения точно фиксируются на дорожках качения.
Для предотвращения «закусывания» крупных подшипников при монтаже или в процессе эксплуатации перед установкой их в разъемные корпуса допускается производить расшабривание поверхностей полуотверстий в местах разъема. Полноту прилегания крупных подшипников к посадочным местам в разъемных корпусах проверяют с помощью калибра и краски (отпечатки краски должны составлять не менее 75% общей посадочной площади). В разъемных корпусах с помощью щупа проверяют также плотность и равномерность прилегания основания крышки (зазор не более 0,03 -0,05 мм).
В собранном узле необходимо проверить наличие зазоров между вращающимися и неподвижными деталями. Особое внимание следует обратить на наличие зазоров между торцами неподвижных деталей и торцами сепараторов, которые иногда выступают за плоскость торцов колец.
Следует проверить также совпадение проточек для подачи смазки в корпусах со смазочными отверстиями в наружных кольцах подшипников.
Для подшипников с цилиндрическими роликами и без бортов после монтажа должно быть проверено относительное смещение наружного и внутреннего колец в осевом направлении. Оно не должно быть более 0,5-1,5 мм для подшипников с короткими роликами и более 1-2 мм - для подшипников с длинными роликами (большие значения даны для подшипников больших размеров).
После завершения сборочных операций и введения в подшипниковые узлы смазочного материала, предусмотренного технической документацией, следует проверить качество монтажа подшипников пробным пуском сборочной единицы на низких оборотах без нагрузки. При этом прослушивают шум вращающихся подшипников с помощью стетоскопа или трубы. Правильно смонтированные и хорошо смазанные подшипники при работе создают тихий, непрерывный и равномерный шум. Свистящий шум свидетельствует о недостаточном смазывании или наличии трения между соприкасающимися деталями узла. Звенящий металлический звук может быть вызван слишком малым зазором в подшипнике. Равномерный вибрирующий звук вызывается попаданием инородных частиц на дорожку качения наружного кольца. Шум, возникающий время от времени при неизменной частоте вращения, свидетельствует о повреждении тел качения. Шум, проявляющийся при изменении частоты вращения, может быть обусловлен повреждением колец в результате монтажа или наличием усталостных выкрашиваний на поверхностях качения. Стучащие звуки возможны вследствие загрязнения подшипника. Неравномерный громкий шум создают сильно поврежденные подшипники.
После эскизной проработки конструкции вала и сопряженных с ним деталей передач подбирают подшипники качения. Конструкция и качество опор определяются типом подшипников, схемой их установки и способом крепления в корпусе и на валу. Это, в свою очередь, зависит от условий работы - величины, направления и характера нагрузки, длины и жесткости вала, вида смазки, защиты от загрязнения; точности изготовления деталей и корпуса (соосности отверстий), качества монтажа, необходимости регулировки и демонтажа подшипников; ресурса (срока службы) подшипников до замены; экономичности, стоимости подшипников и опор в целом. Все это позволяет выбрать тип подшипников и конструктивно оформить опоры.
Выбор типа подшипника. Подшипники - изделия стандартные. При проектировании машин и механизмов их выбирают из каталожных таблиц (см. табл. П.5...П.15).
При выборе типоразмера подшипника для заданного диаметра вала d и условий работы следует учитывать: величину, направление и характер действующей нагрузки; частоту вращения вала; необходимый ресурс работы в час; особые требования, зависящие от конструкции узла или машины и условий их эксплуатации; стоимость подшипника.
В табл. 8.1 приведены эскизы подшипников, наиболее часто применяемых в практике машиностроения.
В соответствии с установившейся практикой проектирования иэксплуатации машин тип подшипников и схему их установки выбирают по следующим рекомендациям.
Для опор валов цилиндрических прямозубых и косозубых колес редукторов применяют чаще всего шариковые радиальные подшипники (табл. 8.1, п.1). Первоначально назначают подшипники легкой серии. При чрезмерно больших размерах шариковых подшипников в качестве опор валов цилиндрических колес применяют подшипники конические роликовые (табл. 8.1, п.4).
Таблица 8.1. Подшипники качения основных типов.
Таблица 8.2. Предварительный выбор подшипников
Таблица 8.3. Ориентировочные зависимости размеров внутренней конструкции подшипников для вычерчивания эскизов и чертежей
Шариковые радиальные подшипники характеризуются малой осевой жесткостью. Поэтому в силовых передачах для опор валов конических и червячных колес применяют конические роликовые подшипники (табл. 8.1, п.4). Первоначально выбирают легкую серию.
Для опор вала конической шестерни принимают по тем же соображениям конические роликовые подшипники. При высокой частоте вращения вала-шестерни (п >1500 мин -1) принимают легкую серию.
Опоры червяка в силовых червячных передачах нагружены значительными осевыми силами. Поэтому в качестве опор вала червяка принимают в основном конические роликовые подшипники. При длительной непрерывной работе червячной передачи с целью снижения тепловыделений применяют также шариковые радиально-упорные подшипники (табл. 8.1,
Для опор плавающих валов (червяки при расстоянии между опорами l > 200 мм, шевронные передачи) применяют радиальные подшипники шариковые или с короткими цилиндрическими роликами с одной стороны (плавающая опора), а с другой спаренные радиально-упорные (см. рис. 8.1).
Схемы установки подшипников. В большинстве случаев валы должны быть зафиксированы в опорах от осевых перемещений. По способности фиксировать осевое положение вала опоры разделяют на плавающие и фиксирующие.
Плавающие опоры допускают осевое перемещение вала в любом направлении для компенсации его удлинения (укорочения) при температурных деформациях. Они воспринимают только радиальную силу. В качестве плавающих опор применяют шариковые и роликовые радиальные подшипники, типы которых показаны в табл. 8.1.
Фиксирующие опоры ограничивают осевое перемещение вала в одном или в обоих направлениях. Они воспринимают радиальную и осевую силы. В качестве фиксирующих опор применяют шариковые и роликовые подшипники, типы которых показаны в табл. 8.1.
В схемах (рис. 8.1, г, д, е) одна опора фиксирующая, вторая - плаваю щая. Фиксирующая опора ограничивает осевое перемещение вала в обоих направлениях. В опоре может быть установлен один или два подшипника, которые закрепляют в осевом направлении с двух сторон как на валу, так и в корпусе. В плавающей опоре внутреннее кольцо подшипника закреплено с двух сторон на валу, а наружное - свободно перемещается в корпусе вдоль оси.
В таком виде (см. рис. 8.1, г, д, е) вал с опорами представляет собой статически определимую систему и может быть представлен в виде балки с одной шарнирно-неподвижной и одной шарнирно-подвижной опорами.
Схемы (рис. 8.1, г, д, е) применяют при любом расстоянии между опорами вала.
При выборе плавающей и фиксирующих опор по схемам (рис. 8.1, г, д, е) учитывают рекомендации:
Подшипники обеих опор должны быть нагружены по возможности равномерно, поэтому если на вал действует осевая сила, то плавающей выбирают опору, нагруженную большей радиальной силой. При этом всю осевую силу воспринимает подшипник, менее нагруженный радиаль- ной силой.
При отсутствии осевых сил плавающей выполняют менее нагружен- ную опору, чтобы уменьшить сопротивление осевому перемещению подшипника и изнашивание поверхности корпуса.
Рис. 8.1. Принципиальные схемы установки подшипников и их фиксирование на валах и корпусе
3. Если входной (выходной) конец вала соединяют с другим валом муфтой, то фиксирующей принимают опору вблизи этого конца вала.
В схемах (см. рис. 8.1, б, в) обе опоры фиксирующие, причем каждая опора фиксирует вал в одном направлении. В опорах этих схем могут быть установлены подшипники: шариковые или роликовые радиальные (см. рис. 8.2, б и 8.2, г) и радиально-упорные (см. рис. 8.2, в).
Указанные схемы применяют с определенными ограничениями по расстоянию 1 п между опорами. Связано это с изменением зазоров в подшипниках при температурных деформациях валов.
В схеме (см. рис. 8.2, а), называемой схемой установки подшипников "враспор" (от осевых сил в сечениях вала между опорами действуют напряжения сжатия), чтобы не происходило защемления тел качения вследствие нагрева при работе, предусматривают осевой зазор а (на рис. не показан). Величина зазора должна быть несколько больше ожидаемой тепловой деформации подшипников и вала. Из опыта известно, что в узлах с радиальными шарикоподшипниками при 1 п ≤ 300 мм а = 0,2...0,5 мм. Требуемый зазор а создают при сборке с помощью набора тонких металлических прокладок, устанавливаемых между корпусом и крышкой подшипника.
В схеме (см. рис. 8.1, в), называемой схемой установки подшипников "врастяжку", возможность защемления тел качения подшипников вследствие температурных деформаций вала уменьшается, так как в этой схеме при удлинении вала осевой зазор в подшипниках увеличивается (см. также рис. 8.3). По этой причине расстояние между подшипниками может быть несколько больше, чем в схеме враспор: 1 п ≤ (8..10) d n . Меньшие значения - для роликовых, большие - для шариковых радиально-упорных подшипников. Для шариковых радиальных 1 п ≤ 12 d n .
Конструирование стаканов. Узел конической шестерни с опорами обычно заключают в стакан, при этом он образует самостоятельную сборочную единицу, что упрощает как технологию сборки, так и регулирование осевого положения зубчатых колес.
Крепление подшипников на валах от осевого смещения (см. рис. 8.2, 8.3 и 8.5) осуществляют: концевыми и стопорными шайбами, шлицевыми гайками, установочными винтами, пружинными упорными кольцами.
Регулирование зазоров радиально-упорных подшипников выполняют: набором прокладок, регулировочными винтами и специальными конструктивными приемами.
В зависимости от схемы расположения подшипников стаканы конструируют по одному из вариантов, представленных на рис. 8.4. При установке стакана в корпус с натягом фланец выполняют уменьшенным, без отверстий под винты.
Стаканы
обычно выполняют из чугунного литья
марки СЧ 15, реже из
стали. Толщину стенки
,
диаметрd
и
число z
винтов
крепления стакана
к корпусу принимают в зависимости от
диаметра D
отверстия
стакана под подшипник по следующим
зависимостям:
Рис. 8.2. Схемы установки подшипников:
а, б, в - враспор; г - плавающая; д, е - левая опора плавающая, правая -фиксированная
Вопрос: Для какой цели предусмотрены детали 1...4 ?
Толщину
упорного буртика
1
и толщину
фланца
2
(рис. 8.4) принимают
Высоту
t
упорного
буртика назначают по той же зависимости,
что и высоту
заплечика вала h
(см.
рис. 7.3 и табл. 7.3), диаметр буртика D
1
=
D
- 2
t
.
Диаметр
фланца D
ф
следует выполнять минимальным. Для
этого
принимают с
d
;
h
=
(1,0
... 1,2) d
;
D
ф
= D
a
+
(4,0
... 4,4) d
,
где
d
-
диаметр
винта.
Рис. 8.4. Стаканы подшипников
Иногда на наружной поверхности стакана делают проточку дл: уменьшения длины посадочного участка (см. рис. 8.4, а). Глубин проточки принимают равной 1,0 мм.
Длину посадочных участков принимают равной ширине кольца подшипника. Канавки в отверстиях стаканов делать не следует поскольку выполнять их сложнее, чем на наружной поверхности. Кроме того, они затрудняют установку подшипников.
Стаканы для подшипников вала конической шестерни перемещаю" при сборке для регулирования осевого положения конической шестерни В этом случае посадка стакана в корпус - H7/js6. Другие стаканы поел! их установки в корпус остаются неподвижными, для них применяю" посадки Н7/k 6 или Н7/m6.
Осевое крепление подшипников. При наличии осевой нагрузки на подшипники и для фиксации их на валу в осевом направлении кольца подшипников должны удерживаться на валу и в корпусе от осевого перемещения с помощью различного рода закрепительных устройств Крепление подшипников на валу и в корпусе выбирают в зависимости от значения и направления действия нагрузки, частоты вращения, типа подшипника, требований монтажа и демонтажа узла и производственных возможностей изготовления. Чем больше осевые нагрузки и выше частота вращения вала, тем надежней должно быть осевое крепление колец подшипника.
Наиболее распространенные способы крепления внутренних коли, подшипников от осевого смещения следующие:
пружинными упорными разрезными кольцами 1 и 2 (рис. 8.5, а); этот способ применяют при незначительных осевых нагрузках; размеры колец иканавок для них приведены в табл. 8.4;
Рис. 8.5. Крепление подшипников в редукторах
Таблица 8.4. Кольца пружинные упорные плоские наружные эксцентрические (ГОСТ 13942-86) и канавки для них. Размеры в мм
торцевой шайбой 3 (рис. 8.5, б) - достаточно надежный и простой способ; штифт 4 фиксирует шайбу от поворота относительно вала (размеры см. в табл. 8.5);
шлицевой гайкой 5 и стопорной шайбой 6, внутренний лепесток которой входит в паз вала, а один из наружных отгибают в прорезь гайки после ее затяжки (рис. 8.5, в); это надежный, но относительно дорогой способ, применять который целесообразно при значительных осевых нагрузках, действующих по направлению к гайке (размеры гаек и шайб
Таблица 8.5. Шайбы концевые (ГОСТ 14734-69). Размеры в мм
Таблица 8.6. Гайки круглые шлицевые (ГОСТ 11871-88). Размеры в мм
* Предпочтительные размеры.
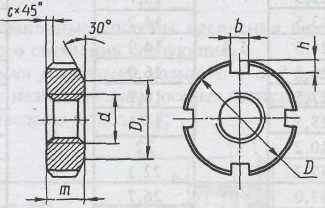
Таблица 8.7. Шайбы стопорные многолапчатые (ГОСТ 11872-89). Размеры в мм
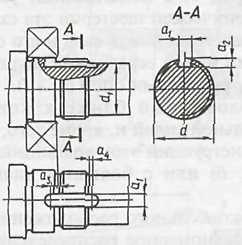
приведены в табл. 8.6 и 8.7, размеры канавок для выхода резьбонарезного инструмента - в табл. 8.8). Осевое крепление наружных колец подшипников осуществляют при помощи заплечиков корпуса (рис. 8.5, в, д) или стакана (рис. 8.5, г), размеры заплечиков можно принимать по тем же рекомендациям, что и для буртиков вала; пружинных колец 2 (см. рис. 8.5, а), конструкция и размеры колец приведены в табл. 8.9; крышек (см. рис. 8.5, а, г).
Кроме изложенных способов для крепления подшипников можно использовать их конструктивные особенности. Например, на рис. 8.5,5 наружное кольцо подшипника выполнено с канавкой для пружинного упорного плоского кольца 3. Преимуществом этого способа является то, что отверстие корпуса не имеет уступа, усложняющего его обработку. Вместе с тем, несущая способность упорного кольца ограничивает восприятие больших осевых сил. На рис. 8.5, в представлена конструкция подшипника с буртиком, которым он удерживается от перемещения вдоль оси.
На рис. 8.5, д показано крепление подшипника в корпусе с помощью трех установочных винтов 8, равномерно расположенных по окружности. Конусные концы винтов воздействуют в трех точках по окружности на кольцо 7. Оно и поджимает подшипник к буртику корпуса. Винты от самоотвинчивания фиксируют замковым кольцом 9.
При конструировании опор конических передач, характерных наличием значительных осевых сил постоянного направления, широко применяют радиально-упорные роликовые или шариковые подшипники (рис. 8.6). На рис. 8.6, а, б, в подшипники установлены по схеме "врастяжку". Для опор конической шестерни эта схема более предпочтительна, так как обеспечивает жесткость вала и его опор при минимально допускаемом расстоянии l между серединами подшипников и увеличенном расстоянии L между реакциями опор (L > l ).
Подшипник, расположенный ближе к конической шестерне, нагружен большей радиальной силой и, кроме того, воспринимает осевую силу. Поэтому в ряде конструкций этот подшипник выбирают более тяжелой серии (рис. 8.6, б) или с большим диаметром посадочного отверстия (рис. 8.6, в). Общим недостатком консольного расположения шестерен (см. рис. 8.6, а, б, в) является неравномерное распределение нагрузки по длине зуба шестерни.
Более рациональным с точки зрения уменьшения неравномерности распределения нагрузки по длине зуба является неконсольное расположение шестерни (рис. 8.6, г). Однако эта конструкция сложнее рассмотренных выше, так как дополнительную опору размещают в стакане или специально выполненной внутренней стенке корпуса редуктора. Радиально-упорные подшипники в этой конструкции установлены «враспор». Как видно из схемы, в фиксирующей опоре расстояние L между реакциями опор меньше расстояния l между серединами
Рис. 8.6. Конструкции подшипниковых узлов конических шестерен
Таблица 8.9. Кольца пружинные упорные плоские внутренние концентрические (ГОСТ 13941-86) и канавки для них. Размеры в мм
Примечание.
Размеры
элементов т
=
1,9 мм, r
0,2
мм, s
=
1,7
мм.
подшипников (L < l ), однако жесткость вала достаточно высокая благодаря наличию второй плавающей опоры.
Cтраница 1
Установка радиально-упорного подшипника с соприкасанием высоких бортов: а - до затяжки, б-после затяжки; о - смещение торцов колец до затяжки, обеспечивающее получение предварительного натяга.
До установки радиально-упорных подшипников осевой разбег составляет 8 - 10 мм. Зазор между деталями ротора и корпуса насоса должен быть по 4 - 6 мм на сторону.
Примеры установки радиально-упорных подшипников, обеспечивающей отсутствие защемления вала при его тепловом расширении, и методы регулировки этих подшипников иллюстрируют фиг.
При установке радиально-упорных подшипников необходимо учитывать линейное удлинение вала при повышении температуры, которое приводит к повреждению подшипника из-за уменьшения осевого зазора. Если расстояние между подшипниками 500 мм (по верхнему пределу), то в рабочем чертеже необходимо давать указание о регулировании подшипников в осевом направлении по наибольшему допустимому осевому зазору для данного типа подшипников. Регулирование осевого зазора производится перемещением наружных колец.
При установке радиально-упорных подшипников в обеих опорах червяка (рис. 21.5) возможно защемление тел качения в результате повышения температуры червяка.
При двух типовых вариантах установки радиально-упорных подшипников (рис. 4) плечи реакций получаются существенно различными (/ - (J / 2), что при нагрузке моментом предопределяет жесткость узла. При определении нагрузки на подшипник в случае парной установки учитывают осевую составляющую.
При двух типовых вариантах установки радиально-упорных подшипников (рис. 4) плечи реакций получаются существенно различными (li У что при нагрузке моментом предопределяет жесткость узла. При определении нагрузки на подшипник в случае парной установки учитывают осевую составляющую.
Вал установлен на конических роликоподшипниках. крышки врезные.| Установка двух радиально-упорных подшипников, поставленных. |
На рис. 9.20 показаны две схемы установки радиально-упорных подшипников, поставленных враспор и врастяжку.
Для компенсации теплового удлинения вала при установке радиально-упорных подшипников следует брать приведенные в табл. 81 несколько расширенные значения осевого зазора.
Аналогичные посадки (за исключением посадки С3п) применяют при установке радиально-упорных подшипников.
L 400 мм показаны на рис. 12.25 и 12.27. При установке радиально-упорных подшипников в распор следует учитывать температурные удлинения вала, чтобы не было защемления тел качения. Конические роликоподшипники обеспечивают большую жесткость валов по сравнению с ра-диально-упорными шарикоподшипниками, но потери на трение в них в 3 - 4 раза выше. В связи с этим при больших частотах вращения червяка целесообразно применять радиально-упорные шарикоподшипники.
Страницы: 1
Схемы установки подшипников
В большинстве случаев валы должны быть зафиксированы в опорах от осевых перемещений. По способности фиксировать осевое положение вала опоры разделяют нафиксирующие и плавающие .
В фиксирующей опоре ограничено осевое перемещение вала в одном или обоих направлениях. Она воспринимают радиальную и осевую силы.
В плавающей опоре осевое перемещение вала в любом направлении не ограничено. Она воспринимают только радиальную силу.
В схемах на рис.6 вал зафиксирован в одной (левой на рисунке) опоре: в схеме на рис.6,а - одним подшипником; в схеме на рис.6,б - двумя однорядными подшипниками. В плавающей опоре применяют обычно радиальные подшипники. Эти схемы применяют при любом расстоянии l между опорами вала. Назначая фиксирующую и плавающую опоры, стремятся обеспечить примерно равную нагруженность подшипников и наименьшие силы трения в плавающей опоре
Рис.6. Схемы установки подшипников Рис.7. Схемы установки подшипников
В схемах на рис.7 - обе опоры фиксирующие.
Различают схемы «в распор» (рис. 7,а). В рассматриваемой конструктивной схеме каждая из опор ограничивает осевое перемещение вала только в одном направлении. Для этого торцы внутренних колец обоих подшипников упирают в торцы буртиков вала (или в торцы других деталей, расположенных на валу). Внешние торцы наружных колец подшипников упирают в торцы подшипниковых крышек (или в торцы других деталей, установленных в посадочном отверстии подшипникового гнезда корпуса).
Схема установки вала «в распор» конструктивно является наиболее простой. Она широко применяется для коротких валов (l/d = 6…8).
Для исключения защемления вала в опорах предусматривают осевой зазор «а », величина которого должна быть несколько больше ожидаемой тепловой деформации подшипников и вала. Из опыта эксплуатации этот зазор устанавливают в пределах 0,2…0,5 мм . Схема с фиксацией подшипников «в распор» удобна в монтаже, но требует жёстких допусков на линейные размеры и опасна возможным защемлением тел качения при нагреве.
При установке вала «в растяжку» (рис.7,б) наружное кольцо подшипника устанавливают с упором в торец заплечика корпусной детали - стакана. Дополнительное крепление кольца с противоположной стороны не делают. Осевой зазор «а »в подшипниках при увеличении температуры вала увеличивается (вероятность защемления подшипников уменьшается). Поэтому расстояние между подшипниками можно брать несколько больше, а именно l/d = 8…10. Более длинные валы по схеме «в растяжку» устанавливать не рекомендуется из-за возможности появления недопустимых для радиально-упорных подшипников осевых зазоров.
Особенности монтажа подшипников качения
1. Радиальные роликоподшипники с одним съемным кольцом без бортов монтируют раздельно - съемное кольцо и кольцо в комплекте с роликами. При наличии на валу в обеих опорах подшипников такого типа необходима дополнительная опора (подпятник) для фиксации вала в осевом направлении. При наличии одного бурта на съемном кольце с целью фиксации вала в обоих направлениях роликоподшипники ставят враспор, т.е. с буртами в разных направлениях.
2. Игольчатый подшипник без колец (т.е. комплект игл) устанавливают на шейку вала, предварительно обильно покрытую пластичным смазочным материалом, а затем надевают корпус. При установке игольчатого подшипника без внутреннего кольца сначала в наружное кольцо набивают пластичный смазочный материал, устанавливают в нее иглы, вводят внутрь монтажную втулку диаметром на 0,1-0,2 мм меньше диаметра вала, затем в таком виде подводят к торцу вала и надвигают с втулки на вал.
3. Подшипники, устанавливаемые на вал на разрезной закрепительной втулке, фиксируют затягиванием гайки. Степень затяжки во избежание защемления тел качения из-за деформации внутреннего кольца проверяют свободным вращением от руки наружного кольца.
4. Одинарные упорные подшипники монтируют следующим образом: кольцо с меньшим внутренним диаметром устанавливают на вал, а с большим - в корпус. У двойного упорного подшипника промежуточное кольцо с меньшим внутренним диаметром монтируют на вал, а боковые кольца с большим внутренним диаметром - в корпус. При установке упорных подшипников зазор между наружным диаметром колец и корпусом в целях обеспечения самоустановки подшипника должен составлять от 0,5 до 1 мм.
5. Радиально-упорные подшипники со съемным наружным кольцом монтируют раздельно: в корпус - наружное кольцо, на вал - внутреннее кольцо с телами качения и сепаратором.
6. Радиально-упорные подшипники с целью восприятия ими осевой нагрузки обоих направлений ставят парами навстречу друг другу.
Осевые зазоры в упорных подшипниках:
Серия подшипника |
Допускаемые пределы зазора (мкм) при диаметре вала (мм) |
|||
до 30 |
от 30 до 50 |
от 50 до 80 |
от 80 до 120 |
|
Легкая |
30-80 |
40-100 |
50-120 |
60-150 |
Средняя и тяжелая |
50-110 |
60-120 |
70-140 |
100-180 |
Предварительный натяг в подшипниках создается с целью устранения радиального и осевого биений узла (например, шпинделя) для повышения точности и виброустойчивости осуществляется следующими способами:
1. установкой прокладки нужной толщины между внутренними (или наружными) кольцами двух радиально-упорных шарикоподшипников с последующим стягиванием наружных (или внутренних) колец до исчезновения просвета между ними;
2. применением сдвоенных радиально-упорных шарикоподшипников, у которых одна пара колец соприкасается, а между другой парой колец имеется зазор, путем стягивания этих колец до исчезновения зазора;
3. установкой между наружными и внутренними кольцами пары шарикоподшипников двух втулок или прокладок различной высоты и последующим стягиванием колец до выборки зазора;
4. нажатием на наружное кольцо подшипника при неподвижном внутреннем с помощью витых или тарельчатых пружин.
Величину натяга в подшипниках контролируют по моменту сопротивления проворачиванию вала; момент может быть найден как произведение усилия, приложенного к динамометру, закрепленному на конце намотанной на вал веревки, на половину диаметра вала.
Регулировку осевого зазора (осевой «игры») радиально-упорных подшипников, необходимого для их правильной работы, осуществляют следующими способами:
1. За счет изменения толщины прокладки или комплекта прокладок между крышкой, прижимающей наружное кольцо подшипника, и корпусом. Толщину прокладки находят путем затягивания винтов крышки без прокладки до получения необходимой «игры» в опорах, измеряемой индикатором, приставленным к торцу вала или посаженной на него детали. С помощью щупа или свинцовой проволоки измеряют зазор между крышкой и корпусом, в соответствии с которым подбирают прокладку или комплект прокладок нужной толщины. Винты крышки могут быть затянуты до полной выборки зазоров в подшипнике, и тогда искомая толщина прокладки будет равна сумме зазора между крышкой и корпусом и требуемого зазора в подшипнике. Регулировочная прокладка может находиться также между крышкой и наружным кольцом подшипника.
2. Перемещением наружного кольца подшипника установочным винтом, ввинченным в крышку, через промежуточную шайбу. Сначала винт при отвернутой контргайке затягивают до отказа, а затем отворачивают на нужную долю оборота в зависимости от требуемого зазора и шага резьбы и стопорят контргайкой.
3. Перемещением наружного кольца подшипника регулировочной гайкой, ввернутой в корпус. Сначала гайку, освобожденную от стопора, затягивают до отказа, а затем несколько отворачивают до создания нужного зазора в подшипнике и стопорят.
4. Перемещением внутреннего кольца подшипника с помощью гайки или винтов и шайбы. После достижения нужного зазора в подшипнике гайку или винты стопорят деформируемыми шайбами.
5. Деформацией внутреннего кольца подшипника, имеющего конусное отверстие, за счет перемещения его гайкой по конусу вала
Регулировку осевого зазора упорных подшипников производят смещением кольца, расположенного в корпусе, с помощью прокладок и другими способами, описанными выше.
Схемы установки подшипников в опорах.
1. Одна из опор фиксирована в осевом направлении, а другая - плавающая. Осевая нагрузка, действующая на вал, воспринимается только фиксированной опорой. Плавающей обычно выполняется опора с меньшей радиальной нагрузкой. В фиксированной опоре внутреннее кольцо подшипника с одной стороны упирается в заплечик вала, а с другой зажимается гайкой, разрезным пружинным кольцом, втулкой и шайбой. Наружное кольцо с одной стороны упирается в заплечик корпуса или стакана, а с другой прижимается крышкой, разрезным пружинным кольцом и гайкой с наружной резьбой.
При значительных осевых нагрузках на вал фиксированную опору составляют из двух радиально-упорных подшипников. В плавающей опоре внутреннее кольцо подшипника крепится так же, как в фиксированной опоре, а наружное кольцо может свободно перемещаться в осевом направлении в расточке корпуса или в стакане.
Данная схема позволяет обеспечить любое расстояние между опорами, компенсировать неточности изготовления деталей узла по длине и тепловое удлинение вала. Применяется обычно при значительных расстояниях между опорами.
2. Крепление подшипников враспор. Внутренние кольца обоих подшипников упираются в заплечики вала, а с другой стороны не крепятся. Наружные кольца располагаются в гладких (без заплечиков) расточках корпуса и лишь с внешней стороны прижимаются крышкой или гайкой с наружной резьбой. Расстояние между опорами при этой схеме ограничено и обычно не превышает 6-8 диаметров опор. Во избежание заклинивания подшипников при нагреве и удлинении вала при монтаже должен быть предусмотрен соответствующий зазор.
Осевые зазоры в радиально-упорных подшипниках
Тип подшипника |
Интервал внутренних диаметров |
Крепление по одному подшипнику в фиксированной и в плавающей опорах |
Крепление враспор по одному подшипнику в обеих опорах |
|
Наибольшее возможное расстояние между опорами |
Допускаемые пределы осевой «игры», мкм |
|||
Шариковый, |
10-30 |
20-40 |
8 опор |
30-60 |
Шариковый, угол контакта α=26-36° |
10-30 |
20-30 |
||
Конический роликовый, |
10-30 |
20-30 |
12 опор |
20-80 |
Конический роликовый, |
10-30 |
20-40 |
Разновидностью данной схемы является конструкция, где внутренние кольца зажимаются с внешней стороны, а изнутри не крепятся. Наружные кольца упираются с внутренней стороны в заплечики стакана или корпуса, а снаружи не крепятся. Конструкция с регулировкой зазора по внутренним кольцам исключает опасность защемления тел качения даже при валах значительной длины.
Каждая из опор при креплении подшипников враспор воспринимает осевую нагрузку только одного направления. По данной схеме устанавливают все радиально-упорные подшипники, а также радиальные шариковые и роликовые с двумя буртами на наружном и одним на внутреннем кольцах.