Цель работы
В процессе работы ознакомиться с назначением, устройством и работой цилиндрического зубчатого редуктора, с конструкцией и регулировкой подшипниковых узлов, смазкой зубчатых колес и подшипников, определить основные параметры зубчатых передач.
Описание редуктора
Зубчатые редукторы - это механизмы, служащие для понижения угловых скоростей и увеличения крутящего момента, выполненные в виде отдельных сборочных единиц.
В качестве отдельных узлов механических передач в конструкциях строительных машин широко применяют смонтированные в едином корпусе закрытые зубчатые или червячные передачи, предназначенные для понижения угловой скорости ведомого вала по сравнению с ведущим валом и называемые редукторами .
Подобные устройства, повышающие угловую скорость, называют ускорителями илимультипликаторами .
По типу передач различают редукторы с цилиндрическими (рис. 1, а-г ), коническими и смешанными коническо-цилиндрическими зубчатыми парами (рис. 1, д ),а также с червячными передачами (рис. 1, е ).
По числу ступеней передач различают редукторы одноступенчатые (рис. 1, а, е ) имногоступенчатые , чаще двух - (рис. 1, в , д )и трехступенчатые (рис. 1, б, г ).
Одноступенчатые цилиндрические редукторы обеспечивают передачу вращательного движения с передаточным числом до 8...10, а конические - с передаточным числом до 5... 6. Наибольшее распространение имеют двухступенчатые цилиндрические редукторы с передаточными числами 8...50 и одноступенчатые червячные редукторы.
|
Редукторы могут быть специальными и универсальными. Специальные редукторы проектируют применительно к конкретной модели машин. Универсальные редукторы , выпускаемые серийно, могут быть установлены на любой машине.
Серийные редукторы выбирают по каталогам заводов-изготовителей в соответствии с передаваемой мощностью, числом оборотов ведущего вала, передаточным числом, межосевым расстоянием (между осями ведущего и ведомого валов), а также другими характеристиками, учитывающими режимы нагружения.
Двухступенчатый цилиндрический редуктор Ц2У (рис. 2) состоит из корпуса 1 , с крышкой 2 , крышкой смотрового окна 3 , отдушиной 4 , пробки маслослива 5 , маслоуказателя 6 , шайбы маслоотражательной 7 , установочного конического штифта 8 , валов 9 , зубчатых колес 10 , подшипников 11 , крышек подшипников, регулировочных колец и других деталей.
Корпусы редукторов чаще всего выполняются литыми из серых чугунов средней прочности СЧ 15-32 и СЧ 18-36, зубчатые колеса и валы - из конструкционных сталей. Корпуса редукторов с межосевым расстоянием тихоходной ступени до 160 мм могут быть отлиты из алюминиевого сплава АЛII.
Зубчатые колеса 10 соединяют с валом 9 посредством шпонок – призматических, клиновых или сегментных стержней, шлицевых соединений – равномерно расположенных по окружности цилиндрической поверхностям вала и ступицы пазов и выступов.
Опоры валов выполняются с применением подшипников качения (шариковых и роликовых) или скольжения .
Назначение опор - удерживать вращающиеся детали в нужном для правильной работы положении. Внутренние кольца подшипников насаживаются на валы с натягом, а наружные кольца, сопрягаемые с неподвижной деталью - корпусом редуктора, устанавливаются с небольшим зазором (или меньшим натягом, чем у внутреннего кольца).
Установка наружного кольца подшипника по скользящей посадке (посадка с зазором) позволяет кольцу во время работы поворачиваться, что обеспечивает более равномерный износ дорожек качения.
В редукторах общего назначения обычно применяется комбинированное смазывание (картерное смазывание). Одно или несколько зубчатых колес смазываются погружением в ванну с жидким смазочным материалом в нижней части корпуса редуктора (картере), а остальные узлы и детали, в том числе подшипники качения, смазываются за счет разбрызгивания масла погруженными колесами и циркуляции внутри корпуса образовавшегося масляного тумана. По времени - это непрерывное смазывание. Картерное смазывание применяют при окружных скоростях погруженных колес до м/с.
Глубина погружения цилиндрических зубчатых колес устанавливается не более (0,8-1,5) -шага зацепления, но не менее 10 мм. При меньших скоростях, например, в тихоходных ступенях многоступенчатых редукторов, допустимо более глубокое погружение колес (до 1/3 радиуса колеса).
Ориентировочно объем масла в ванне можно принимать в пределах (0,3...0.7) 10 -3 м 3 на 1 кВт передаваемой мощности.
При картерном смазывании заправка корпуса редуктора отфильтрованным маслом производится через люк или отверстие, закрываемое резьбовой пробкой - отдушиной, которая обеспечивает также сообщение внутренней полости корпуса с атмосферой, предотвращая возникновение внутри корпуса избыточного давления или вакуума при изменении температуры передачи. Пробка - отдушина завинчивается непосредственно в корпус в верхней его части или в крышку смонтированного люка.
Контроль уровня масла при заправке и эксплуатации производится с помощью маслоуказателей: прозрачных, жезловых, контрольных пробок с цилиндрической или конической резьбой и др.
Поскольку допустимый уровень масла в редукторах может изменяться в весьма ограниченных пределах, из прозрачных маслоуказателей наиболее удобны в применении круглые. Они компактны, просты в изготовлении, однако из-за загрязнения в них со временем снижается видимость уровня. На стержне жезлового маслоуказателя имеются риски, указывающие верхний и нижний уровень масла в картере. Иногда жезловые маслоуказатели одновременно выполняют роль отдушины.
Резьбовые пробки больших размеров применяются в качестве сливных, т.е. закрывающих сливное отверстие. Они располагаются непосредственно у днища корпуса, чтобы с маслом сливался и осадок. Максимальная температура масла в редукторах не должна превышать 95° С.
Для индивидуального смазывания узлов, например, подшипниковых, применяются масленки.
Для предотвращения вытекания смазочного материала из корпуса редуктора или выноса его в виде масляного тумана и брызг применяют различные уплотняющие материалы и устройства. Разъёмы составных корпусов (корпус - крышка) герметизируют специальными мазями, наносимыми на плоскости разъёма перед сборкой корпуса. Во фланцевых соединениях могут применяться также мягкие листовые прокладочные материалы.
В настоящее время для герметизации фланцевых соединений широко применяют уплотнения (ГОСТ 9833) в виде резиновых колец круглого сечения.
Для герметизации мест выхода из корпуса валов диаметром Ø 6...500 мм широко применяются резиновые манжетные уплотнения (ГОСТ 8752). Манжеты предотвращают вытекание масла из корпуса и препятствуют попаданию в него пыли и влаги извне. Металлический каркас в виде пружины придаёт жесткость манжете и позволяет обеспечить плотную и герметичную посадку ее в корпус. Рабочая кромка манжеты прижимается к валу за счет упругих сил резины и браслетной пружины, которая располагается в желобе воротника и представляет собой обычную витую пружину с соединенными между собой концами. Пыльник предохраняет рабочую кромку от попадания пыли и грязи. Манжеты этих типов могут работать при окружной скорости вала у рабочей кромки манжеты до 20 м/с.
В практике имеют применение и другие типы уплотнения валов: с помощью сальниковых войлочных колец, торцовые уплотнения с прижимными дисками, лабиринтные уплотнения и др.
Тип и общие сведения о редукторе заносятся в таблице отчета лабораторной работы (приложение 1).
3. Определение параметров цилиндрического зубчатого редуктора (исходные данные приведены в приложении 4).
1. Определение параметров зубчатых передач.
Определение параметров прямозубых () и косозубых передач: с некоррегированным зацеплением (с нулевым смещением ) или с высотным коррегированным (равносмещенное ) можно выполнять в следующей последовательности:
1.1. Измеряются штангенциркулем размеры (рис. 3) и определяются межосевые расстояния первой (быстроходной) и второй (тихоходной) передачи:
Если величины и близки к стандартным (табл. 1), то они округляются до стандартных величин.1.4. Определяются торцовые модули зубчатых передач.
Курсовая работа
Дисциплина Детали машин
Тема «Расчёт редуктора»
Введение
1. Кинематическая схема и исходные данные
2. Кинематический расчет и выбор электродвигателя
3. Расчет зубчатых колес редуктора
4. Предварительный расчет валов редуктора и выбор подшипников
5. нструктивные размеры шестерни и колеса
6. Конструктивные размеры корпуса редуктора
7. Первый этап компоновки редуктора
8. Проверка долговечности подшипника
9. Второй этап компоновки. Проверка прочности шпоночных соединений
10. Уточненный расчет валов
11. Вычерчивание редуктора
12. Посадки шестерни, зубчатого колеса, подшипника
13. Выбор сорта масла
14. Сборка редуктора
Введение
Редуктором называют механизм, состоящий из зубчатых или червячных передач, выполненный в виде отдельного агрегата и служащий для передачи вращения от вала двигателя к валу рабочей машины. Кинематическая схема привода может включать, помимо редуктора, открытые зубчатые передачи, цепные или ременные передачи. Указанные механизмы являются наиболее распространенной тематикой курсового проектирования.
Назначение редуктора – понижение угловой скорости и соответственно повышение вращающего момента ведомого вала по сравнению с ведущим. Механизмы для повышения угловой скорости, выполненные в виде отдельных агрегатов, называют ускорителями или мультипликаторами.
Редуктор состоит из корпуса (литого чугунного или сварного стального), в котором помещают элементы передачи – зубчатые колеса, валы, подшипники и т. д. В отдельных случаях в корпусе редуктора размещают также устройства для смазывания зацеплений и подшипников (например, внутри корпуса редуктора может быть помещен шестеренный масляный насос) или устройства для охлаждения (например, змеевик с охлаждающей водой в корпусе червячного редуктора).
Редуктор проектируют либо для привода определенной машины, либо по заданной нагрузке (моменту на выходном валу) и передаточному числу без указания конкретного назначения. Второй случай характерен для специализированных заводов, на которых организовано серийное производство редукторов.
Кинематические схемы и общие виды наиболее распространенных типов редукторов представлены на рис. 2.1-2.20 [Л.1]. На кинематических схемах буквой Б обозначен входной (быстроходный) вал редуктора, буквой Т – выходной (тихоходный).
Редукторы классифицируют по следующим основным признакам: типу передачи (зубчатые, червячные или зубчато-червячные); числу ступеней (одноступенчатые, двухступенчатые и т. д.); типу – зубчатых колес (цилиндрические, конические, коническо-цилиндрические и т. д.); относительному расположению валов редуктора в пространстве (горизонтальные, вертикальные); особенностям кинематической схемы (развернутая, соосная, с раздвоенной ступенью и т. д.).
Возможности получения больших передаточных чисел при малых габаритах обеспечивают планетарные и волновые редукторы.
1. Кинематическая схема редуктора
Исходные данные:
Мощность на ведущем валу транспортера
;Угловая скорость вала редуктора
;Передаточное число редуктора
;Отклонение от передаточного числа
;Время работы редуктора
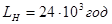
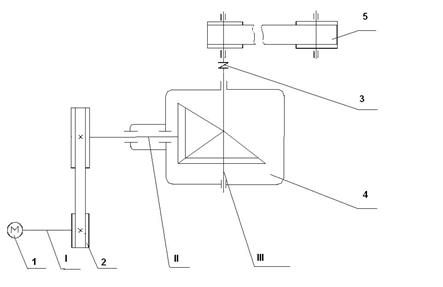
1 – электромотор;
2 – ременная передача;
3 – муфта упругая втулочно-пальцевая;
4 – редуктор;
5 – ленточный транспортёр;
I – вал электромотора;
II – ведущий вал редуктора;
III – ведомый вал редуктора.
2. Кинематический расчет и выбор электродвигателя
2.1 По табл. 1.1 коэффициент полезного действия пары цилиндрических зубчатых колес η 1 = 0,98; коэффициент, учитывающий потери пары подшипников качения, η 2 = 0,99; КПД клиноременной передачи η 3 = 0,95; КПД плоскоременной передачи в опорах приводного барабана, η 4 = 0,99
2.2 ОбщийКПДпривода
η = η 1 η2 η 3 η 4 = 0,98∙0,99 2 ∙0,95∙0,99= 0,90
2.3 Требуемая мощность электродвигателя
= =1,88 кВт.где P III -мощность выходного вала привода,
h-общий КПД привода.
2.4 По ГОСТ 19523-81 (см. табл. П1 приложениях [Л.1]) по требуемой мощности Р дв = 1,88кВт выбираем электродвигатель трехфазный асинхронный короткозамкнутый серии 4А закрытый, обдуваемый, с синхронной частотой вращения 750 об/мин 4А112МА8с параметрами Р дв = 2,2кВт и скольжением 6,0%.
Номинальная частота вращения
n дв.= n c (1-s)
где n c -синхронная частота вращения,
s- скольжение
2.5 Угловая скорость
= = 73,79рад/с.2.6 Частота вращения
= = 114,64об/мин2.7Передаточное отношение
== 6,1где w I -угловая скорость двигателя,
w III -угловая скорость выходного привода
2.8 Намечаем для редуктора u =1,6; тогда для клиноременной передачи
= =3,81– что находиться в пределах рекомендуемого2.9 Крутящий момент, создаваемый на каждом валу.
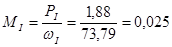
Крутящий момент на 1-м валу М I =0,025кН×м.
P II =P I ×h p =1,88×0,95=1,786 Н×м.
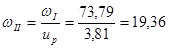
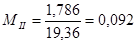
Крутящий момент на 2-м валу М II =0,092 кН×м.
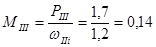
Крутящий момент на 3-м валу М III =0,14 кН×м.
2.10 Выполним проверку:
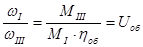
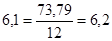
Определим частоту вращения на 2-м валу:
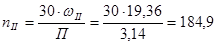
Частоты вращения и угловые скорости валов
3. Расчет зубчатых колес редуктора
Выбираем материалы для зубчатых колес такие же, как в § 12.1 [Л.1].
Для шестерни сталь 45, термообработка – улучшение, твердость НВ 260; для колеса сталь 45, термообработка – улучшение, твердость НВ 230.
Допускаемое контактное напряжение для прямозубых колес из указанных материалов определим с помощью формулы 3.9, , стр.33:
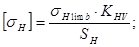
где s H limb – предел контактной выносливости;
b – база нагружения;
K HV – коэффициент долговечности;
S H - коэффициент безопасности.
Значение s H limb выбираем из табл.3.2, стр.34.
Для шестерни:
s H limb =2HB 1 +70=2×260+70=590 МПа;
Для колеса
s H limb =2HB 2 +70=2×230+70=530 МПа.
Для шестерни
= МПа;Для колеса
= МПа.Допускаемое контактное напряжение принимаю
= 442 МПа.Принимаю коэффициент ширины венца ψ bRe = 0,285 (по ГОСТ 12289-76).
Коэффициент К нβ , учитывающий неравномерность распределения нагрузки по ширине венца, примем по табл. 3.1 [Л.1]. Несмотря на симметричное расположение колес относительно опор, примем значение этого коэффициента, как в случае несимметричного расположения колес, так как со стороны клиноременной передачи действует сила давления на ведущий вал, вызывающая его деформацию и ухудшающая контакт зубьев: К нβ = 1,25.
Внешний делительный диаметр колеса находим по формуле (3.9) стр.49
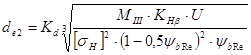
В этой формуле для прямозубых передач К d = 99;
Передаточное число U=1,16;
М III -крутящий момент на 3-м валу.

Принимаем по ГОСТ 12289-76 ближайшее стандартное значение d e 2 =180 мм
Примем число зубьев шестерни z 1 =32
3.1 Число зубьев колеса
z 2 =z 1 ×U=32×1,6=51
3.2 Внешний окружной модуль

3.3 Уточняем значение
мм3.4 Углы делительных конусов
ctqd 1 =U=1,6 d 1 = 32 0
d 2 =90 0 -d 1 =90 0 -32 0 =58 0
3.5 Внешнее конусное расстояние
мм3.6 Длина зуба
мм3.7 Внешний делительный диаметр
мм3.8 Средний делительный диаметр шестерни
мм3.9 Внешние диаметры шестерни и колеса (по вершинам зубьев)
мм мм3.9 Средний окружной модуль
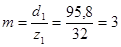
3.10 Коэффициент ширины шестерни по среднему диаметру
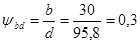
3.11Средняя окружная скорость

Для конических передач обычно назначают 7-ю степень точности.
3.12 Для проверки контактных напряжений определяем коэффициент нагрузки

По табл. 3.5 при ψ bd =0,28;консольним расположением колес и твердости НВ < 350 коэффициент учитывающий распределение нагрузки по длине зуба, К Нβ = 1,15.
Коэффициент, учитывающий распределение нагрузки между прямыми зубьями, К H a =1,05 см. таб. 3.4
Коэффициент, учитывающий динамическую нагрузку в зацеплении, для прямозубых колес при u£ 5 м/с, К H u =1,05 cм. таб. 3.6
Таким образом, К н = 1,15×1,05×1,05 = 1,268.
3.13 Проверяем контактные напряжения по формуле (3.27) из
= 346,4 МПа,346,4<=442 МПа
Условие прочности выполнено
3.14 Силы, действующие в зацеплении:
Окружная
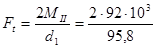
радиальная
592,6 Н; 370 H3.15 Проверим зубья на выносливость по напряжениям изгиба по формуле(3.31) из :
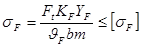
3.16 Коэффициент нагрузки
K F = K F β ∙K F u
3.17 По табл. 3.7 при ψ bd = 0,28,консольном расположении, валах на роликовых подшипниках колес и твердости НВ < 350 значение K Fβ = 1,37.
3.18 По табл. 3.8 при твердости HB<350, скорости u=1,02 м/с и 7-й степени точности коэффициент K F u =1,25(значение взято для 8-й степени точности в соответствии с указанием стр.53
Таким образом, K F u =1,37×1,25=1,71
3.19 Коэффициент, учитывающий форму зуба, Y F зависит от эквивалентного числа зубьев;
у шестерни
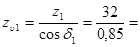
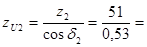
при этом коэффициенты Y Fl = 3,72 и Y F 2 = 3,605 (см. с. 42) .
3.20 Определяем допускаемое напряжение при проверке зубьев на выносливость по напряжением изгиба:
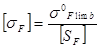
По таб.3.9 для стали 45 улучшенной при твердости HB<350
s 0 Flimb =1,8 HB
Для шестерни σ
= 1,8 260 = 468 МПа;Для колеса σ
= 1,8∙230 = 414 МПа.3.21Коэффициент запаса прочности = "∙""
По табл. 3.9 ¢ = 1,75 для стали 45 улучшенной; коэффициент " = 1 для поковок и штамповок. Следовательно, = 1,75.
3.22 Допускаемые напряжения:
для шестерни [σ F 1 ] =
= 236,5 МПа;для колеса [σ F 2 ] =
= 206 МПа.Проверку на изгиб следует проводить для того зубчатого колеса, для которого отношение
меньше. Найдем эти отношения:для шестерни
= 64 МПа.для колеса
= 57 МПа3.23 Проверку на изгиб проводим для колеса:
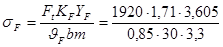
Условие прочности выполнено.
4. Предварительный расчет валов редуктора и выбор подшипников
Предварительный расчет валов на кручение, выполняют по пониженным допускаемым напряжениям.
4.1 Крутящие моменты в поперечных сечения валов:
Ведущего М II =92×10 3 H×м
Ведомого М III =140×10 3 Н×м
4.2 Определим диаметр выходного конца вала при допускаемом напряжении =20 МПа для ведущего вала:
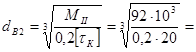
Принимаем ближайшие большее значение из стандартного ряда d B 2 = 28
Диаметр вала под подшипниками принимаем d П2 = 35 мм,
Диаметр под шестерни d K 2 =28 мм
4.3 Определим диаметр выходного конца вала при допускаемом напряжении =15 МПа для ведомого вала:
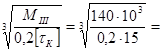
Принимаем ближайшие большее значение из стандартного ряда d B 3 = 38 мм.
Диаметр вала под подшипниками принимаем d П3 = 45 мм.
Диаметр под зубчатым колесом d K 3 =50 мм
Диаметр под уплотнитель d=40 мм
5. Конструктивные размеры шестерни и колеса
5.1 Шестерня:
Сравнительно небольшие размеры шестерни по отношению к диаметру вала позволяют не выделять ступицу. Длина посадочного участка (назовем его по аналогии l ст.).
l ст. =b= 30 мм
5.2 Колесо:
Коническое колесо кованое.
Его размеры: d ае2 =184 мм; b 2 = 30 мм.
Диаметр ступицы d ст = l,2·d k 2 = 1,2 · 50 = 60 мм; длина ступицы l ст = (1,2
l,5)d k 2 = (1,2 1,5) ∙ 28 = 33,6 ÷42 мм, принимаем l ст = 38 мм.Толщина обода δ 0 = (3
4) m = (3 4)∙3 = 9 12 мм, принимаем δ 0 = 10 мм.Толщина диска С =(0,1÷ 0,17) R e =(0,1÷0,17)·105=10,5÷17,9 мм
Принимаем с=14 мм.
6. Конструктивные размеры корпуса редуктора
6.1 Толщина стенок корпуса и крышки:
δ = 0,05·R e +1=0,05·105+1=6,268 мм; принимаю δ=7 мм
δ 1 =0,04·R e +1=0,04·105+1=5,21 мм; принимаю δ=6 мм.
6.2 Толщина фланцев поясов корпуса и крышки:
верхнего пояса корпуса и пояса крышки
b = 1,5 δ = 1,5∙7 = 10,5 мм; принимаю b=11 мм
b 1 = 1,5∙δ 1 = 1,5∙6= 9 мм;
нижнего пояса корпуса
р = 2,35 δ = 2,35∙7 = 16,45 мм; принимаю р = 17 мм.
6.3 Диаметр болтов:
фундаментных d 1 = 0,055R e +12=0,055·105+12=17,79 мм; принимаю фундаментальные болты с резьбой М18;
болтов, крепящих крышку к корпусу у подшипника,
0,75)d 1 = (0,7 0,75)∙18 = 12,0 13,5 мм;принимаю болты с резьбой М12;
болтов, соединяющих крышку с корпусом,
0,6) d 1 = (0,5 0,6)∙18 = 9 10,8 мм;принимаю болты с резьбой М10.
7. Первый этап компоновки редуктора
Компоновку обычно проводят в два этапа. Первый этап служит для приближенного определения положения зубчатых колес относительно опор для последующего определения опорных реакций и подбора подшипников.
Выбираем способ смазывания: зацепление зубчатой пары – окунанием зубчатого колеса в масло; для подшипников – пластичный смазочный материал. Раздельное смазывание принято потому, что один из подшипников ведущего вала удален, и это затрудняет попадание масляных брызг. Кроме того, раздельная смазка предохраняет подшипники от попадания вместе с маслом частиц металла.
Камеры подшипников отделяем от внутренней полости корпуса мазе удерживающими кольцами.
Устанавливаем возможность размещения одной проекции – разрез по осям валов – на листе формата А1. Предпочтителен масштаб 1:1. проводим посредине листа горизонтальную осевую линию – ось ведущего вала. Намечаем положение вертикальной линии – ось ведомого вала. Из точки пересечения проводим под углом δ 1 =32 о осевые линии делительных конусов и откладываем на них отрезки R e =105 мм.
Конструктивно оформляем по найденным выше размерам шестерню и колесо. Вычерчиваем их в зацеплении. Ступицу колеса выполняем несимметрично относительно диска, чтобы уменьшить расстояние между опорами ведомого вала.
Подшипники валов расположим в стаканах.
Намечаем для валов роликоподшипники конические однорядные легкой серии (см. таблица П7):
Наносим габариты подшипников ведущего вала, наметив предварительно внутреннюю стенку корпуса на расстоянии 8-10 мм от торца шестерни и отложив зазор между стенкой корпуса и торцом подшипника для размещения мазеудерживающего кольцо 10-15 мм.
При установке радиально-упорных подшипников необходимо учитывать, что радиальные реакции считают приложенными к валу в точках пересечения нормалей, проведенных к срединам контактных площадок (см. табл. 9.21). для однорядных конических роликоподшипников по формуле:
мм.Размер от среднего диаметра шестерни до реакции подшипника
f 1 =d 1 +a 1 =35+15,72=50,72 мм
Принимаем размер между реакциями подшипников ведущего вала
с 1 ~(1,4÷2,3)· f 1 = (1,4÷2,3)· 50,72=7 1÷ 116 , 6 мм
Принимаем с 1 =90 мм.
Размещаем подшипники ведомого вала, наметив предварительно внутреннюю стенку корпуса на расстоянии 10-15 мм от торца ступицы колеса и отложив зазор между стенкой корпуса и торцом подшипника 15-20 мм для размещения мазеудерживающего кольца.
Для подшипников 7209 размер

Определяем замером размер А – от линии реакции подшипника до оси ведущего вала. Корпус редуктора выполнен симметричным относительно оси ведущего вала и примем размер А = А = мм. Нанесём габариты подшипников ведомого вала.
Замером определяем расстояния f 2 = мм и с 2 = мм (так как А`+А=f 2 +c 2).
Очерчиваем контур внутренней стенки корпуса, отложив зазор между стенкой и зубьями колеса, равный 1,5 х, т.е. 15мм.
8. Проверка долговечности подшипника
8.1 С точки зрения конструктивных соображений более рациональным будет просчитать долговечность наиболее нагруженного подшипника на валу, который вращается с большей частотой, т.е. подшипник находящейся радом с шестерней на ведущем валу.
Из предыдущих расчетов имеем F t = 1920 H, F r =592,6 H; F a =370 Н из первого этапа компоновки с 1 = 90 мм. и f 1 = 50.72 мм
Реакции опор:
в плоскости xz
R x 2 c 1 – F t f 1 = 0 H ;
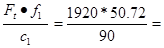
R x1 c 1 – F t (f 1 +c 1)= 0 H ;

Проверка: R x 2 – R x 1 + F t = 1082 – 3002 + 1920 = 0 H;
в плоскости yz
R y2 + F r f 1 - F a
= 0 H; 137 H ;R y1 + Fr*(f1 + c 1) - F a
= 0 H; 729,6 H;Проверка:
H;Суммарные реакции:
Н; Н;Осевые составляющие радиальных реакций конических подшипников [формуле (9.9)]
S 2 = 0.83eP r2 = 0.83*0.37*1090,6=334 H;
S 1 = 0.83eP r1 = 0.83*0.37*3089,5 = 948,8 H;
здесь для подшипников 7207 параметр осевого нагружения e = 0,37
Осевые нагрузки подшипников (см. табл. 9,21) [ Л. 1.] В нашем случае S 1 >S 2 ; F a >0; тогда P a 1 = S 1 = 1002.4 H; P a 2 = S 1 + F a =1002.4 +370=1372.4 H
Рассмотрим левый подшипник
Отношение P a 1 / P r 1 = 948.8/3089.5 = 0.307>e, поэтому не следует учитывать осевую нагрузку.
Эквивалентная нагрузка Р э1 =VР r 1 K б K T , в которой радиальная нагрузка Р r 1 = 3089,6 Н; V = 1; коэффициент безопасности для приводов ленточных конвейеров K б = 1 (см. табл. 9.19) [Л.1]; К T = 1 (см. табл. 9.20) [Л.1].
Р э2 = 3089,6 Н.
Расчетная долговечность, млн. об [формула (9.1)]
млн. обРасчетная долговечность, ч
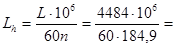
Найденная долговечность приемлема так, как требуемая долговечность намного меньше, чем расчетная долговечность подшипника.
9. Второй этап компоновки редуктора
В развитие первой компоновки здесь вычерчивают валы с насаженными на них деталями; размеры мазеудерживающих колец, установочных гаек и шайб, крышек и уплотнений определяют в соответствии с таблицей в гл IX [Л.1.]; размеры шпонок – в соответствии с таблицей в гл VII [Л.1.].
Диаметры участков валов под зубчатые колёса, подшипники и пр. назначают в соответствии с результатами предварительного расчета м с учетом технологических требований на обработку и сборку.
Взаимное расположение подшипников фиксируем распорной втулкой и установочной гайкой М х 1,5 со стопорной многолапчатой шайбой. Толщину стенки втулки назначают (0,1 – 0,15)d п; прнимаем её равной 0,15*35= 5,25мм.
Мазеудерживающие кольца устанавливают так, чтобы они выходили за торец стакана или стенки внутрь корпуса на 1-2 мм.
Подшипники размещаем в стакане, толщина стенки которого
ст =(0,08-0,12)D,где D- наружный диаметр подшипника;
ст =0,12*728 мм.Для фиксации наружных колец подшипников от осевых перемещений у стакана сделан упор величиной К=6 мм.
У второго подшипника наружное кольцо фиксируем торцовым выступом крышки подшипника через распорное кольцо.
Для облегчения посадки на вал подшипника, прилегающего к шестерне, диаметр вала уменьшаем на 0,5-1 мм на длине. несколько меньшей длинны распорной втулки.
Очерчиваем всю внутреннюю стенку корпуса, сохраняя величины зазоров, принятых в первом этапе компоновки: х=10 мм, и у 2 =20 мм и др.
Используя расстояния f 2 и с 2 , вычерчиваем подшипники.
Для фиксации зубчатое колесо упирается с одной стороны в утолщение вала
мм, а с другой – в мазе удерживающее кольцо; участок вала 50 мм делаем короче ступицы колеса, чтобы мазеудерживающее кольцо 45 мм упиралось в торец колеса, а не в буртик вала; преход вала от 50мм к 45мм смещен на 2-3 мм внутрь зубчатого колеса.Наносим толщину стенки корпуса
к = 7 мм и определяем размеры основных элементов корпуса в соответствии с главой X [Л.1.]Проверка прочности шпоночных соединений
Шпонки призматические со скругленными торцами. Размеры сечений шпонок и пазов и длины шпонок – по ГОСТ 23360 – 78 (см. табл. 8.9) .
Методические указания
к лабораторной работе № 5
по деталям машин для студентов
машиностроительных специальностей
всех форм обучения
Нижний Новгород 2006
Составители А.А. Ульянов, Л.Т. Крюков, М.Н.Лукьянов
УДК 621.833: 539.4 (075.5)
Определение основных параметров зубчатого цилиндрического редуктора: Метод. указания к лабораторной работе №5 по деталям машин для студентов машиностроительных спец. всех форм обучения / НГТУ; Сост.: А.А. Ульянов, Л.Т. Крюков, М.Н. Лукьянов - Н. Новгород, 2006. – 19 с.
Составлено в соответствии с ГОСТ 2.105-95 ЕСКД и СТП 1-У-НГТУ-98 для оформления текстовой документации на изделия машиностроения.
Научный редактор Н.В. Дворянинов
Подписано в печать Формат 60х84 1 /16. Бумага газетная.
Печать офсетная. Печ. л. 1,25. Уч.- изд. л. 1,2. Тираж. Заказ
Нижегородский государственный технический университет.
Типография НГТУ, 603600, Н. Новгород, ул. Минина, 24.
© Нижегородский государственный
технический университет, 2006
1 ЦЕЛЬ ЛАБОРАТОРНОЙ РАБОТЫ
Целью данной работы для студентов является
– изучение конструкции,
– определение основных параметров,
– приобретение навыков разборки, регулирования и сборки
зубчатого цилиндрического редуктора.
2 КРАТКИЕ СВЕДЕНИЯ ИЗ ТЕОРИИ
2.1 Редуктором называется одна или несколько зубчатых (червячных) передач, помещенных в герметичный корпус с масляной ванной и предназ-наченных для понижения угловой скорости и увеличения вращающего момента на выходном валу.
Ступень редуктора – передача, связывающая два соседних вала.
Поток редуктора – передача, передающая один поток мощности.
2.2 В самом общем виде зубчатый редуктор должен иметь:
– передачи зацеплением (шестерни и колеса), валы, опоры валов (подшипники);
– систему регулирования зацеплений и "осевой игры" валов (зазоров в подшипниках);
– корпус и крышку с крепежными деталями и штифтами для фиксации относительного положения корпуса и крышки;
– систему смазки с элементами для заливки, контроля и слива масла;
– уплотнения разъемов, входных и выходных концов валов;
– устройства для выравнивания давления внутри корпуса (отдушина);
– устройства для транспортирования (рым-болты, проушины, крюки и др.
2.2.1 В цилиндрических редукторах применяют в основном косозубые передачи . Зубчатое колесо с меньшим числом зубьев называют шестерней z 1 , с большим числом зубьев – колесом z 2 .
На промежуточных валах направление зубьев шестерни и колеса должны совпадать (для компенсации действия осевых сил). Однако в массовом и крупносерийном производствах оборудование участков для изготовления зубчатых колес специализировано и настроено для нарезания зубьев колес z 2 всех ступеней справым наклоном , а шестерен z 1 – с левым . В этом случае осевые силы в зацеплениях суммируются, увеличивая нагрузку подшипников, но такое "техническое нарушение" в массовом производстве дает большие экономические выгоды, снижая себестоимость изделия за счет уменьшения трудоемкости изготовления без переналадки оборудования.
2.2.2 Так как на натурных редукторах в данной лабораторной работе действительные значения коэффициентов смещения в зацеплениях неизвестны, то последние будем определять только из условия отсутствия подрезания зубьев, и передача будет УСЛОВНО равносмещенной.
Основные параметры косозубыхцилиндрических передач внешнего зацепления:
1) числа зубьев z 1 и z 2 , их суммарное число z S = z 1 + z 2 ;
2) передаточные числа:
– ступеней u = z 2 / z 1: - быстроходной u Б и тихоходной u Т;
– общее редуктора u 0 = u Б u Т;
3) межосевое расстояние a W = 0,5 z S m n /cosb (2.1)
4) ширина зубчатого венца b . Рабочая ширина венца b W = b 2 ;
5) коэффициент рабочей ширины венца по межосевому расстоянию
y ba = b W / a W ;
коэффициент рабочей ширины по начальному диаметру шестерни d W 1
y bd = b W /d W 1 или y bd = 0,5y ba (u + 1).
6) модуль зацепления m = p /p, где р – шаг зубьев по дуге делительной окружности.
Стандартные значения a W , u , y ba для цилиндрических зубчатых передач с внешним зацеплением по ГОСТ 2185 – 66 приведены в приложении А.1; нормальные модули m по ГОСТ 9563 – 60 – в приложении А.2.
Если измерить a W , z S и найти cosb¢ (см. ниже, п.5.7), то по формуле (2.1)
ориентировочно можно определить нормальный модуль m n :
m n ¢ = 2 a W cosb¢/ z S , (2.2)
с округлением его до стандартного значения m , соответствующего m n .
7) Параметры исходного контура цилиндрических зубчатых колес – по ГОСТ 13755-81:
угол профиля a = 20 0 ; высота головки зуба h a = h a *m , где h a *= 1; высота зуба h = 2,25 m ; радиальный зазор в зацеплении с = 0,25 m .
8) После округления модуля по формуле (2.1) уточняется значение угла наклона зубьев b:
b = arccos(0,5 m z S / a W ) . (2.3)
Для косых зубьев [b] = 8...18 0 .
Делительный угол профиля в торцовом сечении
a t = arctg(tg20 0 / cosb). (2.4)
Основной угол наклона зуба
b b = arcsin(sinbcos20 0). (2.5)
9) число зубьев шестерни должно быть проверено на отсутствие подрезания ножки зуба по формуле z 1 ³ z 1 min = 17 cos 3 b.
При невыполнении этого условия следует рассчитать коэффициент смещения х 1 при нарезании зубьев шестерни х 1 = 1 – z 1 / z 1 min при условии z 1 < z 1 min и х 1 > 0. Если z 1 ³ z 1 min , то в данной лабораторной работе условно
следует принять х 1 = 0.
В косозубых и шевронных передачах при малых значениях z 1 рекомендуется высотная коррекция зубьев, т.е. х 2 = – х 1 и х 1 + х 2 = 0.
10) диаметры окружностей (при х 1 + х 2 = 0), мм:
– делительных d = mz / cosb; (2.6)
– начальных d W 1 = 2a W / (u + 1) , d W 2 = d W 1 u ; (2.7)
– вершин d a = d + 2m (1 + x ) ; (2.8)
– впадин d f = d – (2,5 – 2x )m ; (2.9)
11) окружная скорость зубчатых колес v = pd W n / (6×10 4), м/с, (2.10)
где n – частота вращения зубчатого колеса, мин -1 .
2.2.3 Для передачи вращающего момента между валом и колесом служат шпонки , шлицы , штифты и посадки с гарантированным натягом .
Шестерни , как правило, выполняют за одно целое с валом. Колеса – съемные.
Входные и выходные концы валов выполняют коническими по ГОСТ12081 - 72 (предпочтительные) и цилиндрическими по ГОСТ 12080 - 66.
2.2.4 В качестве опор валов используют подшипники качения. В связи с ростом нагрузок и углов наклона зубьев в цилиндрических редукторах общего назначения все чаще и чаще применяют роликовые конические радиально-упорные подшипники .
Система условных обозначений подшипников качения установлена ГОСТ
3189 – 89 и подробно описана в методических указаниях к лабораторной работе № 10 .
В цилиндрических редукторах – валы короткие ; опоры односторонние фиксирующие; схема установки подшипников на валах – "враспор" .
2.2.5 В цилиндрических передачах зацепления специально не регули-руют . Для компенсации погрешностей изготовления и сборки в осевом направлении выполняют b 1 > b 2 . Регулируют зазоры в подшипниках, обеспечивая при сборке "осевую игру" вала. "Осевая игра " – это допусти-мые монтажные осевые зазоры вала в комплекте с подшипниками, необходимые для нормальной работы узла и учитывающие последующие рабочие температурные деформации (выборку зазора).
Регулирование "осевой игры" (зазоров в подшипниках) выполняют при помощи регулировочных прокладок, шлифуемых колец, круглых гаек с многолапчатыми шайбами, винтовых регуляторов, пружин и др. В настоящее время зазоры в роликовых конических подшипниках при их установке "враспор" регулируют винтовыми регуляторами (рисунок 1).
На рисунке 1 обозначено: 1 – вал; 2 – подшипник; 3 – корпус редуктора
4 – нажимная шайба; 5 – врезная крышка подшипникового узла с мелкой метрической резьбой (Md x p ); 6 – регулировочный винт, ввертываемый в крышку специальным ключом через отверстия 7 в винте; 8 – фиксатор от самоотвинчивания винта 6.
Рисунок 1 – Винтовой регулятор "осевой игры"
За один оборот винта 6 (360 0) шайба 4 и с ней наружное кольцо подшипника 2 переместятся в осевом направлении на величину шага резьбы р . Если винт имеет n отверстий 7, то минимально возможный его поворот будет на угол g = 360 0 / n , чему соответствует осевое перемещение регулятора (шайбы) на p / n . Отсюда вывод : чем меньше шаг резьбы р и больше число отверстий n (т.е. диаметры d и d 0), тем выше "чувствительность" регулятора и меньше достижимая величина (выше точность) осевого регулирования зазоров.
2.2.6 В массовом и крупносерийном производствах корпуса и крышки редукторов изготавливают литьем из чугуна, стали или силумина; в единич-ном и мелкосерийном производствах, как правило, – сваркой из стального проката.
Утолщения на корпусных деталях в зонах подшипников называются бобышками . Подшипниковые гнезда снаружи закрывают крышками, которые могут быть накладными (крепятся винтами к корпусу и крышке редуктора) и врезными (вкладываются в проточку корпусных деталей). Врезные крышки более современные и предпочтительные. На крышках устанавливают винтовые регуляторы (рисунок 1).
Выступы для установки крепежных деталей, окантовывающие корпус и крышку по их разъему, называются фланцами . Выступы для крепления корпуса к раме (плите) привода называют лапами .
На бобышках, фланцах, лапах устанавливают винты или болты. Класс прочности болтов должен быть не ниже 6.6. На фланце корпуса выполняют резьбовое отверстие под отжимной болт.
Как правило, окончательная расточка отверстий под подшипники производится за один установ с одной стороны штангой с резцами. Перед расточкой бобышки и фланцы стягивают болтами (винтами), после чего корпус и крышку фиксируют двумя штифтами (расположенными по диагонали), устанавливают на станок и производят расточку отверстий всех валов. Штифты обеспечивают сохранение точности расточки отверстий после разборки и сборки редуктора. Предпочтительными являются конические штифты.
На крышках выполняют проушины для механического транспортиро-вания редукторов. А на тяжелых редукторах – еще и крюки на фланцах корпусов.
2.2.7 Картерное (окунанием) смазывание зубчатых колес применяют при окружной скорости v от 0,3 до 12,5 м/с. Рекомендуемая вязкость масла m для стальных зубчатых колес в зависимости от напряжений s Н и скорости v
Приведена в приложении Б.
Принцип назначения сорта масла: чем больше скорость v , тем меньше требуемая вязкость m, а чем больше напряжения s Н , тем больше должна быть вязкость m.
Для двухступенчатых редукторов выбор m производится по средним значениям величин s Н m и v m быстроходной и тихоходной ступеней.
1) И – индустриальное;
2) Г – для гидравлических систем; Л – легконагруженные узлы; Т – тяжелонагруженные узлы;
3) группа по эксплуатационным свойствам: А – масло без присадок; С – масло с антиокислительными, антикоррозионными и противоизносными присадками и др.;
4) класс кинематической вязкости m.
Например, масло И–Г–А–46, где 46 – средняя кинематическая вязкость m, мм 2 /c, при 40 0 .
Допустимые уровни погружения колес цилиндрического редуктора в масляную ванну h M от 2m до 0,25d 2 T).
Считают, что в двухступенчатой передаче при v ³1 м/с достаточно погружать в масло только колесо тихоходной ступени. При v < 1 м/с в масло должны быть погружены колеса обеих ступеней редуктора.
Минимально необходимый объем масла для смазывания зубчатых передач V min = (0,3 ... 0,7) литра на 1 кВт передаваемой мощности (в среднем V min = 0,5Р л/кВт, где Р –мощность редуктора). Фактический объем масла V в картере определяется по внутренним размерам ванны корпуса L ВН, В ВН и уровню (высоте) масла Н М в ней (V = L ВН х В ВН х Н М дм 3 ; 1дм 3 = 1л). Должно выполняться условие V > V min .
При скорости колеса v > 1 м/с подшипники смазываются разбрыз-гиванием картерного масла. При меньшей скорости применяют пластичные смазки.
Заливка масла осуществляется через смотровой люк или отверстие, закрываемое пробкой–отдушиной, в крышке редуктора. Слив масла – через отверстие с пробкой в днище корпуса.
Контроль уровня масла осуществляют через контрольные пробки, щупами, через стекло и т.д.
2.2.8 Для предотвращения вытекания масла через зазоры во входных и выходных валах применяют манжетные (по ГОСТ 8752-79), торцовые, щелевые, лабиринтные и др. уплотнения .
Для герметизации плоскости разъема корпуса и крышки перед окон-чательной сборкой их покрывают слоем герметика УТ – 34 ГОСТ 24285-80.
2.2.9 В зависимости от взаимного расположения осей валов, количества выходящих из корпуса концов валов (от 2-х до 4-х) и их ориентации в плане по ГОСТ 20373-94 установлены варианты сборки редукторов, которые приведены в приложении А.3.
2.2.10 Пример обозначения цилиндрического двухступенчатого узкого редуктора с межосевым расстоянием тихоходной ступени a W Т = 200 мм, общим передаточным числом u 0 = 25, 12-м вариантом сборки, с коническим концом выходного вала – К, с климатическим исполнением У (умеренный климат), 2-ой категории размещения по ГОСТ Р 50891-96:
РЕДУКТОР Ц2У – 200 – 25 – 12К – У2 ГОСТ Р 50891-96.
То же для одноступенчатого редуктора с a W = 160, u = 3,15, сборка 22:
РЕДУКТОР ЦУ – 160 – 3,15 – 22К – У2 ГОСТ Р 50891-96.
3 ОБЪЕКТ И СРЕДСТВА ВЫПОЛНЕНИЯ РАБОТЫ
Объектами анализа являются одно- или двухступенчатые цилиндри-ческие редукторы промышленного изготовления различных кинематических схем и конструктивных исполнений.
Для выполнения работы в лаборатории преподавателем выдаются конкретный редуктор, слесарный и измерительный инструмент, необходимая методическая и справочная литература.
Для проведения расчетов студент должен иметь микрокалькулятор, а для записи результатов – типовой бланк "Отчета".
4 ОХРАНА ТРУДА
Общие правила по технике безопасности и производственной санитарии для сотрудников и студентов на кафедре изложены в инструкции № 289.
Для данной работы следует подчеркнуть:
1) редукторы и их детали, как правило, имеют значительные массы;
2) при переносе или перестановке редуктора необходимо убедиться, что болты бобышек, фланцев и крышек подшипников затянуты. За концы валов редуктор не поднимать. Поднимать можно за фланцы корпуса;
3) не совать пальцы в зазор плоскости разъема между крышкой и корпусом, в зацепления зубчатых передач;
4) снятые детали редуктора (крышки, валы, колеса и т.д.) необходимо неподвижно и надежно фиксировать на плоскости стола;
5) при разборке крепежные изделия складывать в одном месте;
6) после сборки редуктора валы должны свободно вращаться от руки, не должно оставаться "лишних" деталей; болты должны быть затянуты ключами;
7) при получении травмы немедленно сообщить об этом преподавателю.
5 ПОРЯДОК ВЫПОЛНЕНИЯ РАБОТЫ
5.1 В произвольном масштабе, но с соблюдением основных пропорций,
нарисовать эскиз заданного редуктора в 2-х проекциях. Пример показан на рисунке 2.
5.2 По пунктам таблицы 1 "Отчета" (см. приложение В) измерить и записать габаритные и присоединительные размеры редуктора. Указать их (в конкретных цифрах) на эскизе редуктора (рисунок 1 в "Отчете "). Для справки все параметры таблицы 1 обозначены буквами на рисунке 2. Для конкретных конструкций редукторов они могут видоизменяться или отсутствовать.
5.3 Произвести разборку редуктора и ознакомиться с устройством его деталей, обращая особое внимание на конструктивные особенности зубчатых колес, валов, подшипников, регуляторов, корпуса, крышек, деталей системы смазки, уплотнений и т.п.
5.4 Измерить крепежные болты (винты) и дать их стандартное обозначение.
5.5 На рисунке 2 "Отчета" выполнить кинематическую схему редуктора согласно ГОСТ 2.770-68 ЕСКД.
5.6 Произвести классификацию редуктора по пунктам, указанным в приложении В.
5.7 Используя указания и формулы п.2.2.2, определить основные параметры зацеплений и зубчатых колес в последовательности, указанной в таблице 2 приложения В. Для одноступенчатого редуктора графа "Резуль-таты" таблицы 2 должна иметь только две колонки (z 1 и z 2). В графе "Примечание" указан способ определения параметра (измерением или расчетом). Измерения следует производить с наибольшей достижимой точностью.